As a design guru, the software developer delves into logistics service providers' requirements like no other. He is passionate about exchanging information securely and efficiently and thus speeding up the physical logistics process.
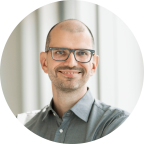
Dispatching is straightforward for special trips, full truck loads (FTL) or less than truck loads (LTL). Many companies who serve this segment don't even have a transport management system. However, as digitalisation progresses, many shippers expect them to provide digital order communication and transparent status management.
Old hands often arrange FTL and special transports with nothing more than a well-filled address book and one or two phone calls. However, their customers, especially in manufacturing, increasingly expect digital processes in order management. This is because these businesses are integrated in a broader planning context. One way to give them a digital, but straightforward, solution is to:
This simple order portal can enable a process that meets the digital demands of their manufacturing clientele within one short month. And they can do it all without a transport management system and the implementation expense it entails.
The most important thing needed for electronic data interchange is a simple database that the company must set up. Customers can send their orders to the database digitally and then receive status updates as their shipments move through the process. It is important to transfer the information to the database seamlessly, thus eliminating the risk of errors. The freight forwarder or carrier, for its part, defines a simple digital workflow that determines when each new status is reached and how it can be set in the system. These building blocks then form the backend for the order portal.
If you are digitalising your processes, you should also make sure that going digital will yield organisational improvements for you. For example, an electronic order file in the database can greatly simplify billing. This is because, the file, along with the quotation, documents all the steps taken as well as the successful delivery. The invoice can thus be issued earlier without needing important data from other systems such as an email client or Excel spreadsheet. In addition, invoices can be sent digitally.
Once a digital order portal is up and running, it starts having the desired outcome. Everyone involved in the process always knows where they currently stand since all the order data is consolidated in a single point of truth. Thanks to an application programming interface (API), the information can even be displayed directly in an industrial customer's operational systems, such as its enterprise resource planning (ERP) system. This significantly improves planning reliability for customers: they now already know about departures from the plan without having to call someone first. It is also possible to integrate mobile apps into the process chain and extract information such as the expected time of arrival (ETA).
An order portal can deliver real, significant benefits for forwarding agents, carriers and their customers for very little effort or expense:
Small cause, big effect. It benefits everyone when service providers and customers digitalise their order communications.
Add a comment