As a college-educated computer scientist, Bastian Späth understands how IT solutions are developed from the ground up. For more than 15 years, he has spent every workday collecting requirements, finding ideas, developing designs, setting up projects and getting them safely across the finish line.
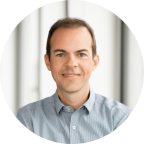
Add a comment